Find issues fast & fix them fast with ENVIROSENSE for Facility Maintenance.
Stay one step ahead with real-time information from every system in your facility. Knowing what’s happening now means discovering what might happen next.
Factory - Facility Maintenance
Benefits
Efficiency
- Routine inspections is reduced when real time monitoring is in place.
- Downtime computation is fully automated with machine generated data.
- Direct access to online reports reduces manual reporting.
- Data analysis can all be done by a single team of experts at the headquarters instead of deploying them at every site.
Transparency
Machine-generated KPIs provide a transparent and accurate measure of maintenance quality and acts as a benchmark for performance evaluation.
FMs who adopt this eMaintenance model are able to win the confidence of their clients by objectively verifying Service Level Agreement commitments in a timely and transparent manner.
Availability
ENVIROSENSE’s 10-level escalating and recurring alerts management system plays the crucial role of:
- Immediately alerting the local technician of failures
- Sending out reminders at predetermined intervals as long as the failure persists.
- Sending out second-level alerts to the supervisor if the downtime exceeds a predetermined threshold.
- Continuing the escalation all the way to the headquarters or the client.
This mean full accountability and alertness across the organization, resulting in high facilities uptime, happy clients, profits, and sustainability.
Maintenance Challenges
Costly inspections are necessary to learn facility status.
Lengthy intervals between problem detection and transmission of the issue to decision-makers.
Cumbersome to check KPIs & Service Level Agreements.
How ENVIROSENSE eMaintenance Works?
Data Acquisition
ENVIROSENSE’s model of eMaintenance functions through the deployment of embedded Internet gateways to extract only relevant maintenance-related information at the source.
It then transmits the data to a central server on the Internet. Similar data from all sites are consolidated, processed, and delivered in real time to the desktops and mobile devices of technicians and decision makers at all levels of management.
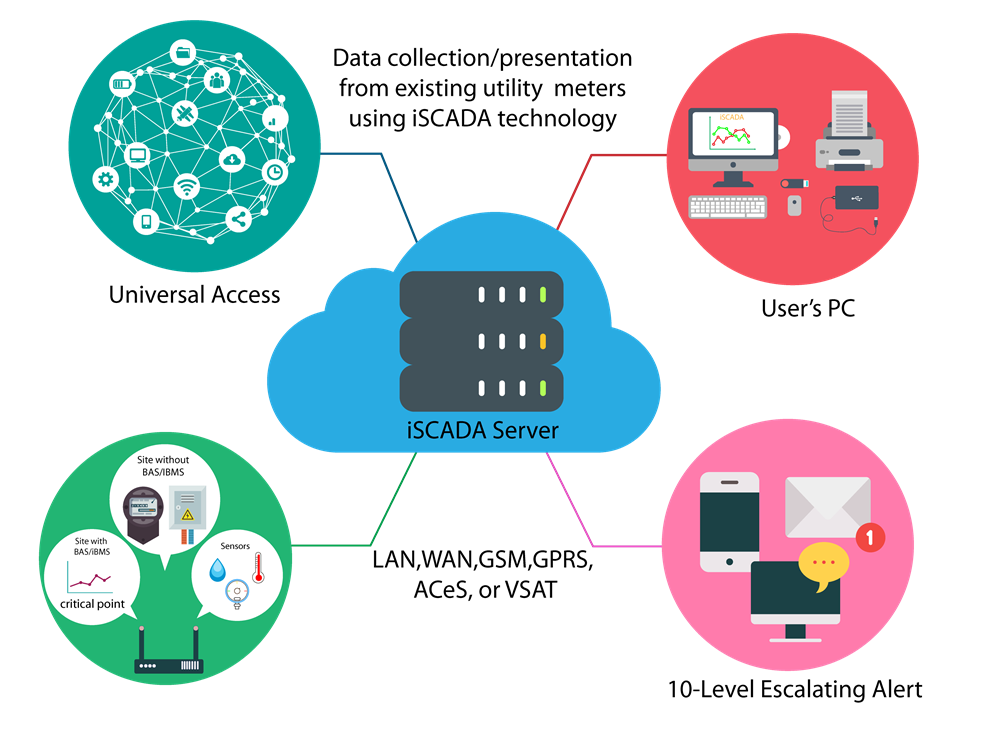
Success Stories
Envirosense Technology has worked with a customer since 2015, and has implemented both the HEPS solution and the Max Demand Control (MDC) solution in its facilities to help with their energy efficiency efforts and with their Maximum Demand mitigation.
By using the data collected from the HEPS installation, and with consultation and advice from Envirosense Technology, they have been able to optimize their production schedule to ensure that they are not incurring any unnecessary Maximum Demand charges, shifting their larger loads to Off-Peak periods to avoid said Max Demand penalties.
From what would have been a Max Demand of 100 Megawatts, they have been able to maintain their MD at 70 Megawatts by utilizing the Max Demand Controller.
By using the Maximum Demand Controller in conjunction with the HEPS solution, customer was able to maintain their MD at a certain level and, by doing so, avoid additional Maximum Demand penalties from the Utility.
As shown above, by setting the MDC at 70MW, they were able to make operational changes to reduce their KW consumption and keep their Max Demand within acceptable parameters.
The yellow line represents their Real Time consumption, while the red bars represent the Max Demand as recorded by the Utility. The HEPS allowed them to view the effect of said changes in real time, enabling Amsteel to make corrections to their efforts as they were being implemented.
By shifting their heaviest consumption to Off Peak periods, they were able to enjoy further benefits such as no MD penalties during Off Peak and reduced Kilowatt Hour costs.
Customer (owner of Steel mills)
Customer is a member of The Lion Group commenced operations in 1988. It operates two steel mills both in Selangor, which are equipped with modern facilities comprising Electric Arc Furnaces of 85-ton and 160-ton respectively, 6-strand Continuous Casting Machines and Ladle Furnaces to produce billets for rolling into bars and wire rods.
The Banting mill produces special grade bars and wire rods for automotive parts, mattress and mechanical springs, turning parts, wire ropes and other specialty uses
Mission Critical Data Centres Multinational
40,000+ Employees Worldwide; Data Centers located in Asia require real-time in-site environmental monitoring and trending. ENVIROSENSE was deployed to monitor UPS system, electrical system, temperature & humidity, precision air conditioners, water detection and fire suppression systems.
Implementation
For implementation, contact us or call +91 8920149032